How To Soundproof A Wooden Garden Studio / Practice Room
A Basic Guide To Studio Soundproofing In 7 Simple Steps
IMPORTANT - We need to make it clear first of all, that soundproofing a wooden structure to studio level, is not an easy task. Because sound is predominantly blocked by mass, by starting with a light weight construction (compared to concrete block for example), you are starting at a much weaker point. This means if you use the same system as a solid building studio, your results will not be as good as in the solid building. If you wish to achieve the same kind of results, you need to go much further.
If you are choosing a timber structure because you think it will be cheaper, it's worth considering the extra cost of upgrading the soundproofing.
This certainly doesn't mean you can't soundproof a timber strucure to a high level, it just means you need to put in more work and investment to reach the same level or have a realistic expectation of your results.
The Seven Steps Of Soundproofing A Timber Music Studio
In this blog we will talk through the details of the following basic steps
- Upgrade The Initial Structure (Optional) - If you have a basic timber structure, you will need to improve it before adding your internal soundproofing. If you alread have a well built room that is already insulated and internally boarded, you may skip this step.
- Build A "Room Within A Room" - An internal room that can contain the airborne sound and vibration.
- Add Resilience - The ability to absorb sound energy and vibration
- Add Mass - Its Mass (weight/density) that blocks airborne sound waves
- Upgrade Windows and Doors
- Power And Lighting - How to install them without creating weaknesses in the soundproofing
- Ventilation - Every studio needs it, but you need to minimize this weak point.
Past Studio Client Videos
Our Guide To Soundproofing Your Timber Garden Room to Studio / Practice Room Level
Here are our 7 basic steps to achieve a high level of soundproofing for high decibel applications. This can be applied to purpose-built or existing timber structures such as garden rooms, summer houses, out houses, barns etc...
Important note: Our studio specifications are based around a specific system. This is a system that is tried and tested and is proven to perform to a high level.
There will always be cheap alternatives, but in our experience, this leads to disappointing results. If you are serious about building your garden studio and want to make a serious reduction in volumes, have a good read through the below info.
If you need further advice about your specific situation, contact us to speak to our dedicated studio soundproofing advisors.
Step One - Increase The Mass And Insulation Of The Timber Structure (Optional)
A lot of timber structures will just have a timber frame and an external cladding. This will be doing very little in the way of soundproofing naturally. If you just install the soundproofing system without improvig this structure, your resutls will be limited.
If you already have a well built garden room or office for example, that is insulated and boarded internally, not just a shed type structure, you can skip to Step Two.
If you have a very basic shed type structure, then read on.
Firstly, you will need to insulate the existing hollow frames. This means the wall frames and between the roof rafters. You can use Thermal Insulation for this stage, however a good acoustic mineral wool will give good thermal insulation and good acoustic insulation.
Secondly, cladd the inside of the structure with heavy, dense material to increase the mass. This can be two layers of 15mm acoustic grade plasterboard, or if you prefer an OSB board, or even better a cement particle board for even more mass.
Step Two- Room Within A Room
Floor - If you have a concrete floor, you don't need to add any more mass. So you can get away with a minimal layer of vibration absorbing matting on the floor. This seperates your floor finish (carpet, laminate etc) from the structural floor (concrete) and absorbs the vibration in between. Height loss will only be around 5 - 10mm. You could use a floor layer such as our ImpactoMat 5mm or for a higher performance, our SoundMat 2 Plus.
Ceiling - Your suspended ceiling can be fixed directly to the bottom of the existing ceiling joists for minimal height loss. As long as the joists are insulated with acoustic mineral wool.
Floor - float timber batons on isolation strips across the floor. Fill between the batons with acoustic mineral wool insulation. Add strips of isolation strip on top of the batons, then add a structural floor layer such as T&G chipboard (18mm / 22mm), then add a soundproofing matting on top to add mass and resilience to the floor. Something like our
SoundMat 3 Plus would be perfect. Then your final floor finish on top.
This will build up your height much more and be more expensive, but performance would be greatly improved if you need it.
Ceiling - Secondary Joists as above.
Step Three - Add Resilience
Resilience gives a material the ability to flex, move and absorb impact and vibration.
It’s the same principle as how the suspension springs in a car give you a more comfortable journey, because the car can absorb the impact of potholes much easier. A rigid car with no suspension would be a far more uncomfortable ride.
By suspending our mass layers on a resilient system, it means that the mass layers (plasterboard and TecSound see Step Four ) can flex, move, and absorb the impact of the sound wave and absorb the vibration energy of the sound.
We use a high-performance resilient system called the
ReductoClip System , which can be fixed to the face of your new stud frames and suspends your mass layers. This is the slimmest resilient system on the market, giving you high performance for minimal space loss.
Step Four - Add Mass
The only thing that blocks the airborne sound wave, is mass .
Mass is basically weight, so the heavier and more dense a material is, the more sound it blocks. Therefore, starting with a structure that is higher in mass is always a better start when possible. A brick or concrete block building will naturally block a higher level of sound than a timber building for example.
We want to cover our new internal wall frames with multiple layers of heavy, dense materials. At the same time, we want to mix different types of material so that we can block a wider range of sound frequencies.
We recommend a combination of acoustic grade plaster board and FlexiSound 5.
We aim to add 35kg of mass per m2.
Ceilings
We use the same ReductoClip resilient system and mass layers for the ceiling to create a soundproof suspended ceiling.
Step Five - Windows and Doors
Step Six - Power and Lighting
Step Seven - Ventilation
A well soundproofed room will be very well insulated and airtight. This will make the room warm and with no natural air flow. Therefore, we need some sort of ventilation system.
This will always be a weakness to a degree as this is basically a hole from the inside to outside but is unfortunately a necessary step.
You can use expensive, digital air conditioning systems and powered ventilation systems if you want, or just a basic in/out . But you will need to insulate any ducting and reduce as much sound from the outlet as you can by using baffles / silencers / attenuators
Two Room Studio (Live Room and Control Room or Multiple Practice Rooms)
Material Cost
Conclusion
"We don’t expect you to become an overnight expert in soundproofing, that’s what we’re here for."
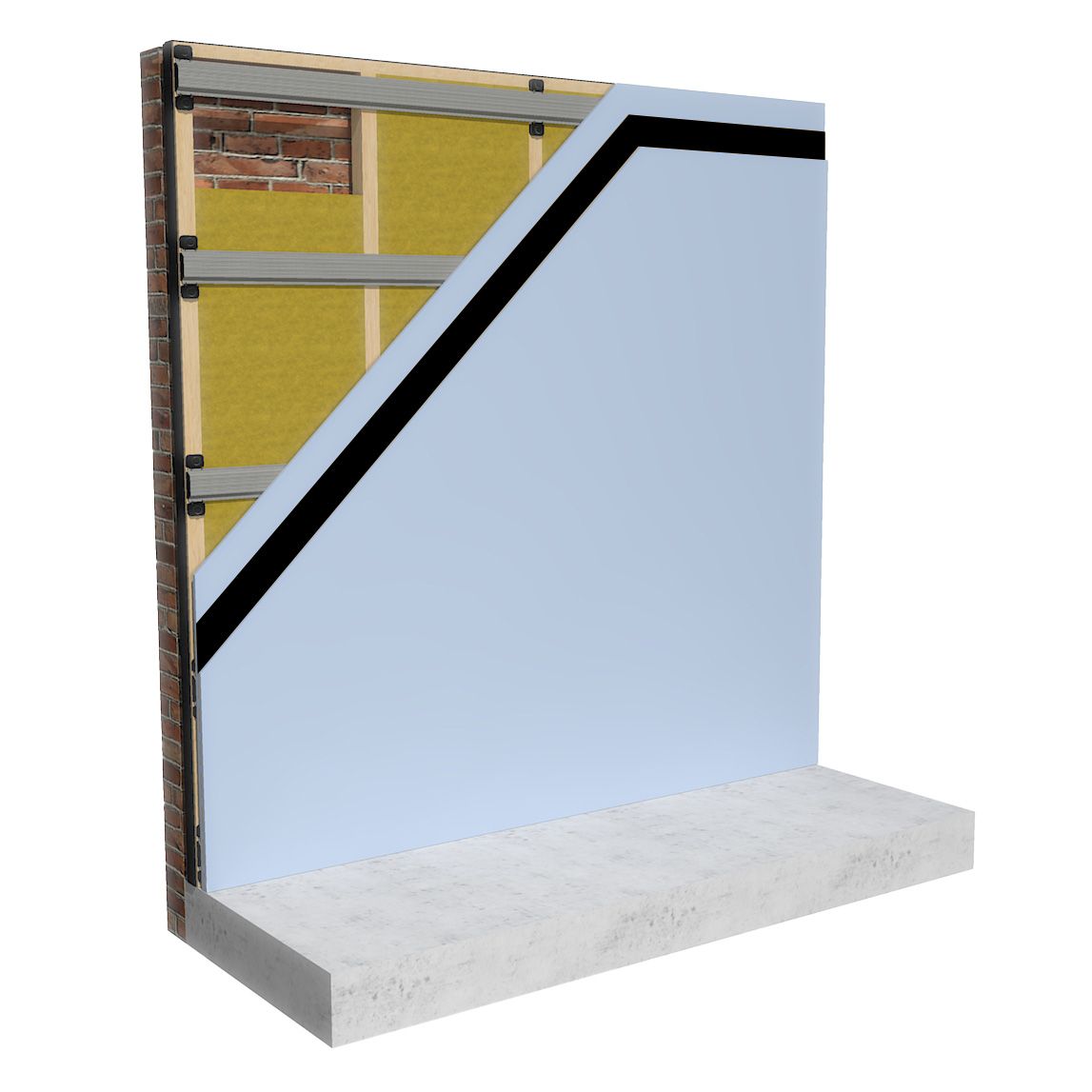